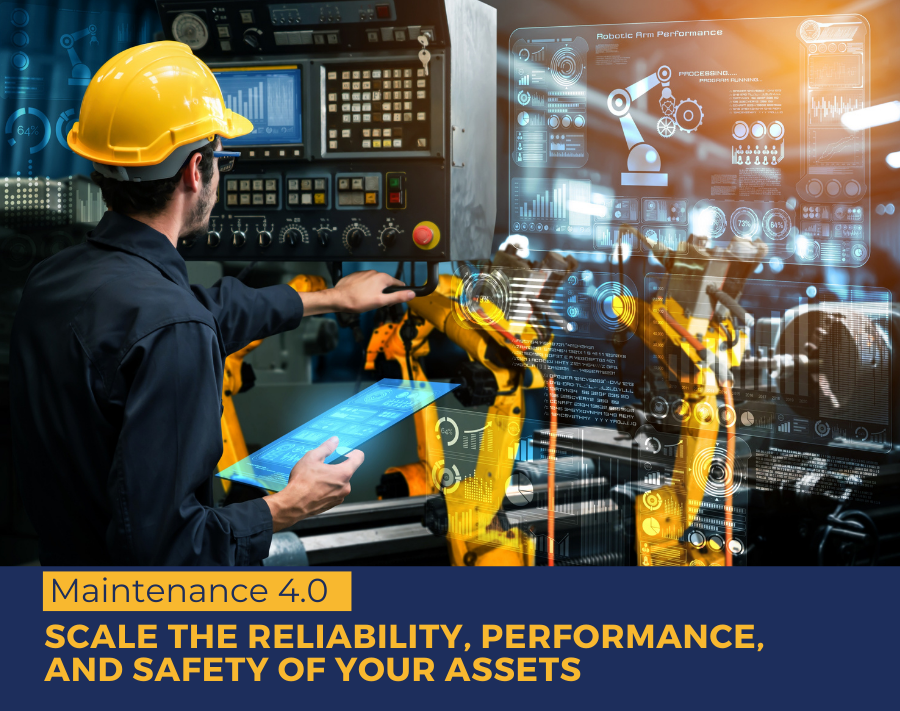
Maintenance 4.0: Scale the reliability, performance, and safety of your assets

Stage Rejigdigital
Digital manufacturing, the fourth industrial revolution aka Industry 4.0 Solutions is the collated technological offering that has revolutionized value creation in the manufacturing industry!
In 2022, the key efficiencies that the manufacturing industry highly seeks are: flexible automation, connectivity and intelligence. These combine to provide optimal industrial production. The vision of Maintenance 4.0 is also to ensure that the production process should be majorly automated.
It began in the 1780’s where the Industry 1.0 was characterized using machines powered by water and steam to the 2020’s where big data, artificial intelligence, Internet of Things join hands to automate formerly manual-only production tasks.
Well then what exactly is the biggest positive of 4.0? Maintenance! Unless and until all the production capabilities are well maintained; achieving optimal production is nearly impossible. But by combining maintenance with the digital transformation solutions like Big Data, Artificial intelligence, Internet of Things, sensors, mobility solutions and more; optimization can be accomplished.
Maintenance 4.0 – Switching from prevention to prediction:
Maintenance 4.0 ensures that maximum data is collected, utilized and then used for predicting certain manual or machine based outcomes.
For instance, a Manufacturing industry 4.0 capacity can combine the strengths of big data and IoT to accurately predict the equipment’s life, risks of failure or downtime and the respective impact these would have. Hence, transitioning the focus from traditionally preventive outlook to contemporary predictive outlook.
Let’s understand a bit more about predictive maintenance. Predictive maintenance provides the two most essential boons:
- predicting deviation in operations and
- predicting possible defects in processes and machines
Both the above predictions, if not timely addressed, can result in downtime and failure which can be irrecoverable at least in the short term. But how does this prediction result in prevention?
Predictive maintenance for risk aversion:
Predictive maintenance is a super smart tool that combines both real-time and historical behaviors to analyze the existing working mechanism. Let’s say, unexpected slowing down of one of the equipment caused a bottleneck and therefore affected the entire supply chain.
Now, this historical data will be used to keep a track of the moment when the speed starts dropping. And as soon as this change is detected (which manually is quite hard to individually track), the systems and representatives are notified. Not just that, the 4.0 advancement will also, to certain extent, correct this deviation automatically and continue its processes. That is how prediction occurs to prevent mishaps.
The key benefits of predictive maintenance in Industry 4.0 are optimized maintenance schedules, early detection and salvation of breakdowns, and significantly reduced downtimes.
Also Read : How IoT will Contribute to the Growth of Industry 4.0 in 2022
The 4 key tools that make up the industry 4.0 solutions especially in the manufacturing industry are:
1. Cloud Computing:
Cloud computing uses servers, storage, databases, networking, software, analytics and intelligence to provide computing services over the internet.
Cloud computing copies the data on multiple redundant sites on the provider’s network. This makes data backup, disaster recovery and business continuity both smoother and less expensive.
2. Internet of Things:
Internet of Things blends technologies and devices to facilitate easy transfer of data between the devices and cloud or even amongst devices themselves. Two of the major ways IoT helps in predictive maintenance is by generating reports in real-time and by highlighting deviations in processes.
Both the above processes, if done manually, would require a huge number of employees resulting in labor costs which can easily be avoided via automation.
3. Big Data:
Big data is a combination of both structured and unstructured data sets collected from newer sources and are voluminous. It is correct to say that traditional data processing softwares would fail to process these data sets.
Big data is used in fields as diverse as manufacturing, medicine, agriculture and environment safety. Big data allows for better decision making, data collection, and real-time operation.
4. Artificial Intelligence:
Artificial intelligence is the ability of machines to think and learn like humans. Its major benefits are deeper data analysis, low human error rates, and improved workflows.
To name a few, here are three crucial ways artificial intelligence helps the manufacturing industry:
– Smarter machines that efficiently automate production processes.
– Estimating process deviations
– Identifying quality defects
Conclusion:
Imagine the combination of these 4 powerful tools and the impact it can have on your business! While 4.0 seems to be rapidly evolving and the updates might seem like the limit of technological improvements; it is highly predicted that industrial revolution 5.0 will come to realization way sooner than expected.
But till then, adapting to the latest 4.0 technologies will keep businesses efficient, profitable and pioneers in the industry. And while you do so, don’t forget to upskill the personnel to make the best use of industry 4.0 solutions. If you want to know more about our IoT-enabled smart manufacturing solutions, then drop us a line at info@rejigdigital.com.